In my previous article, we looked at the logistics of taking over a ship from another management company.
Being a dry bulk man (specialist in dry cargo ships only), I was pleasantly surprised when my Fleet Manager asked me if I would go, takeover and dry dock a 15 year old chemical tanker. Like a true Karunyan, I jumped at the challenge.
The vessel was to be taken over at Baltic port of Ventspils, Latvia on the 12th August 2021. A Captain and a second engineer from my company joined the vessel, in advance, at the port previous to Ventspils and the rest of us joined at Ventspils.
We will not go into the aspects of the vessel takeover as it was detailed in my previous article. We will look at the complex process of dry docking a ship.
Dry docking is the process of taking a ship out of water for carrying out maintenance on the hull which is usually submerged in water.
The ship is literally floated into a large tank which is fitted with a gate. Once the ship is inside, the gates are closed and the water in the enclosed tank is pumped out.
The ship gradually sinks with the falling water level and finally rests on specially prepared concrete blocks, capped with soft wood.
The exposed hull is cleaned of all marine growth such as barnacles, mussels etc., that cling to and grow on it. All these sea organisms greatly impede the the performance of the ship.
Severe hull fouling can also lead to overloading of the vessel’s main engine, thereby resulting in increased fuel consumption and operational costs.
This vessel was a 15 year old chemical tanker, which was owned by an American company.
The company had decided to apply a silicone based hull paint, which was supposed to save fuel costs by as much as 8%.
The hull treatment, along with the special silicone paint would cost the shipowner in excess of half a million dollars. But with a predicted savings of about 8% in fuel costs, this would be quickly earned back. Prior to arriving at this yard, the normal fuel cost of this ship was about USD 15,000 per day. The savings would amount to USD 1200 per sailing day, which was quite substantial .
After taking over the vessel at Ventspils, we set sail to the shipyard in Gdynia, a Polish port also on the Baltic sea. Prior to arrival at the yard, all the cargo tanks needed to be cleaned and inerted. As the vessel had just been taken over from the previous Owners, we took stock of the various issues that needed to be rectified at the shipyard.
The vessel was fitted with 12 cargo tanks, and two slop tanks.
All cargo tanks were washed with hot water, with the help of specially provided tank cleaning machines. Once cleaned, the dirty water was then transferred with the help of the cargo pumps into the slop tank. Standard operating procedure before entering a shipyard: On arriving at the shipyard, the vessel will first anchor outside port limits, where a barge will come alongside the vessel. The dirty water from the slop tanks will then be pumped to the barge, and then the slop tanks will also be cleaned and the remaining dirty water will then be transferred to the barge.
On completion of this operation, a chemist from the shipyard will check the condition of the 12 cargo tanks and two slop tanks with a special instrument. Once he is satisfied that the tanks do not contain any flammable gases, he will then issue a gas free certificate.
Only after this , the vessel will then be allowed to enter the shipyard.
Once inside the yard, a meeting was held with the yard representative, ship’s representative (yours truly) the ship’s senior management team and the vessel Owners’ representatives in attendance..
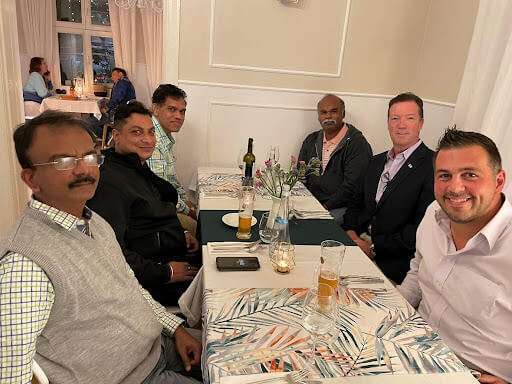
From Left – Niranjan, his colleague, Chief Engineer, the Captain, “big boss”- Mr. David Burke, VP Ridgebury tankers.
All jobs were discussed and the schedule at the shipyard was agreed upon.
The vessel was at the yard for about 30 days and all jobs and surveys were completed as specified.
The silicone paint gleamed in the bright Polish sunshine as the yard personnel demonstrated how water would flow past the hull , with minimum resistance.
It was now time for undocking and seatrials.
For undocking, the docking process was reversed Water was pumped into the tank or dock and as the water level slowly rose, all checks were made by the ship’s staff and me , to ensure the absence of leaks..
Once we were satisfied, the dock was filled to capacity, such that the level of water in the dock was level with the sea outside.
Once this was achieved, the dock gates were opened, and the vessel was slowly and gently towed out.
Once in safe waters, the engines were tested , and the vessel was put out to sea, with a few, select shipyard personnel on board.
After a few hours, satisfied with the results of the sea trials, we disembarked from the vessel, and returned to the hotel, tired but happy with a job well done.
The vessel, now anchored outside the port limits at Gydnia, awaits her next orders for loading.
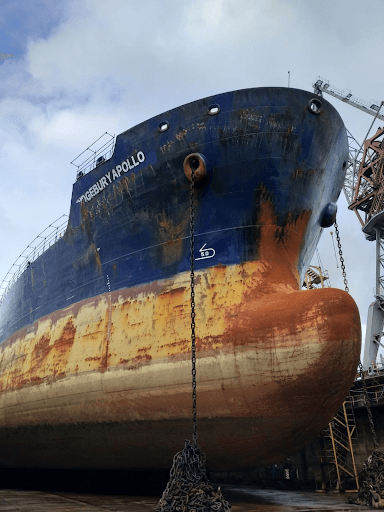
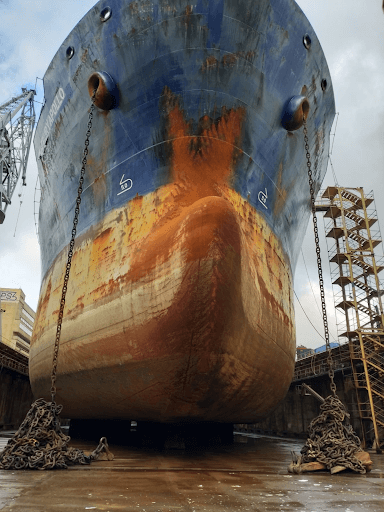
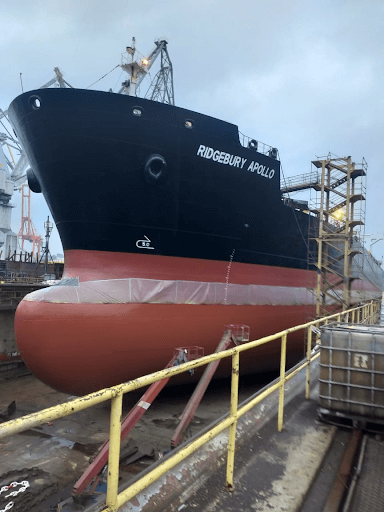